Checking Out the Various Strategies and Technologies Behind Plastic Extrusion
The realm of plastic extrusion is a blend of technology, modern technology, and accuracy, crucial to countless industries worldwide. Advanced machinery, computerized controls, and a selection of products assemble in this complex procedure, creating high-grade, resilient items.
Comprehending the Essentials of Plastic Extrusion
The process of plastic extrusion, typically hailed as a keystone in the realm of manufacturing, creates the bedrock of this conversation. In essence, plastic extrusion is a high-volume manufacturing process in which raw plastic material is thawed and created right into a continual profile. The procedure starts with feeding plastic products, commonly in the type of pellets, into a warmed barrel.
The Function of Various Products in Plastic Extrusion
While plastic extrusion is a frequently used strategy in production, the materials used in this procedure considerably affect its last outcome. Different kinds of plastics, such as pvc, abdominal muscle, and polyethylene, each lend distinct properties to the end item. Polyethylene, known for its durability and adaptability, is typically utilized in product packaging, while PVC, renowned for its strength and resistance to environmental aspects, is made use of in building and construction. ABS, on the other hand, incorporates the best qualities of both, resulting in high-impact resistance and durability. The option of product not only impacts the product's physical residential properties yet additionally influences the extrusion rate and temperature. Manufacturers have to carefully think about the residential or commercial properties of the material to maximize the extrusion procedure.
Strategies Used in the Plastic Extrusion Process
The plastic extrusion process includes various techniques that are important to its procedure and performance (plastic extrusion). The conversation will certainly begin with a simplified description of the essentials of plastic extrusion. This will certainly be followed by a failure of the procedure in detail and an expedition of techniques to boost the performance of the extrusion strategy
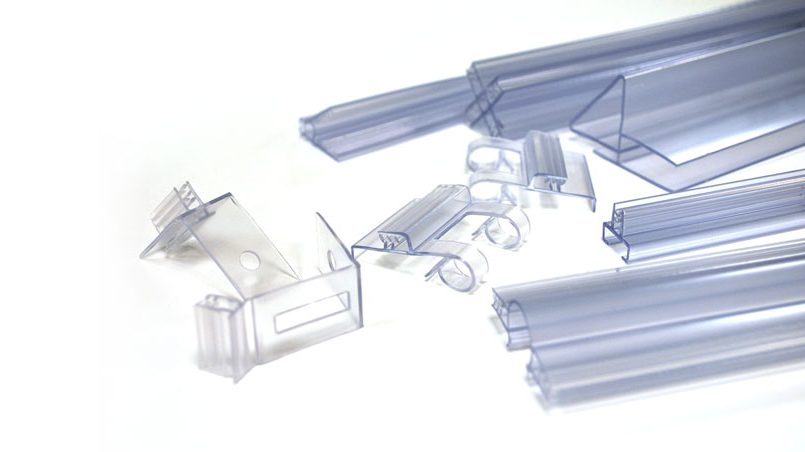
Understanding Plastic Extrusion Fundamentals
In the realm of production, plastic extrusion stands as a fundamental procedure, crucial in the production of a multitude of daily items. At its core, plastic extrusion involves transforming raw plastic product into a continuous profiled shape. This is attained by thawing the plastic, frequently in the kind of pellets or granules, and forcing it via a designed die. The resulting product is a lengthy plastic piece, such as a panel, pipe, or wire coating, that retains the shape of the die. This cost-effective method is very flexible, able to develop intricate shapes and fit a wide range of plastic materials. Fundamental understanding of these essentials permits further expedition of the extra elaborate aspects of plastic extrusion.
Thorough Extrusion Refine Failure
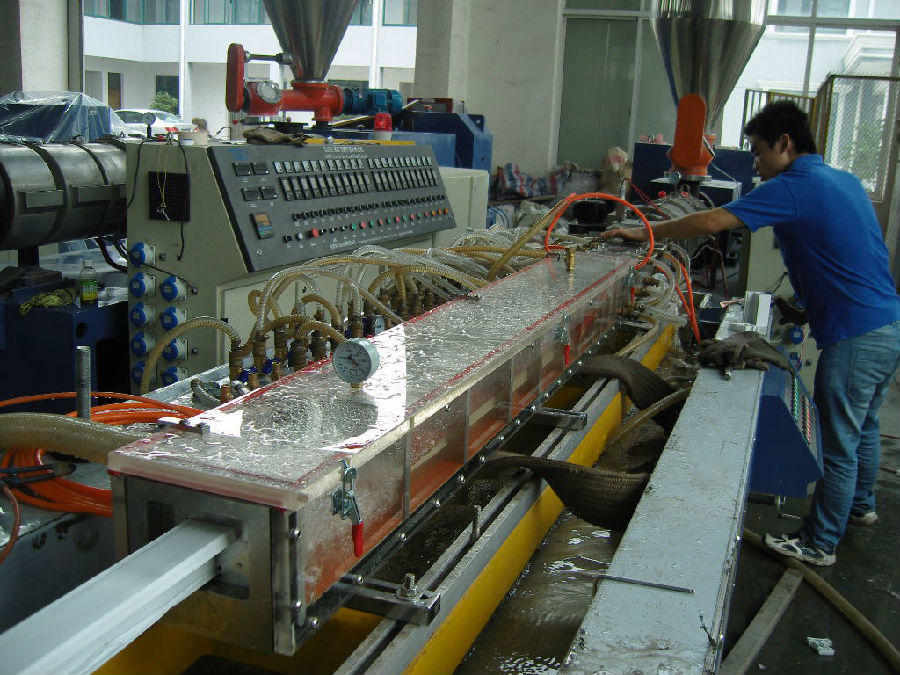
Improving Extrusion Technique Performance
Efficiency gains in the plastic extrusion procedure can significantly influence both the high quality of the final product and the overall efficiency of the operation. Constant optimization of the extrusion strategy is crucial to keeping a competitive side. Techniques that improve Continued performance usually entail exact control of temperature level and pressure throughout the procedure. Modern technologies, such as computerized systems and sensing units, have contributed in achieving this control. In addition, the use of top quality basic materials can reduce waste and boost outcome high quality. Regular upkeep of extrusion tools can likewise minimize downtimes, therefore raising efficiency. Lastly, embracing lean production principles can help get rid of unnecessary action in the process, advertising effectiveness gains.
How Innovation Is Transforming the Face of Plastic Extrusion
The arrival of new technology has actually considerably transformed the landscape of plastic extrusion. It has caused the growth of innovative extrusion machinery, which has actually improved the effectiveness and top quality of the plastic extrusion process. Innovations in the extrusion process have additionally been driven by technical developments, supplying boosted abilities and adaptability.
Advanced Extrusion Equipment
Reinventing the world of plastic extrusion, advanced equipment imbued with advanced technology is ushering in a new period of efficiency and accuracy. These machines, geared up with innovative functions like automatic temperature level control systems, make certain ideal conditions for plastic processing, consequently minimizing waste and improving item top quality. While these advancements are already amazing, the constant advancement of modern technology assures also better jumps onward in the area of plastic extrusion equipment.
Technologies in Extrusion Procedures
Utilizing the power of modern technology, plastic extrusion processes are going through a transformative metamorphosis. Innovations such as computerized numerical control (CNC) systems now enable more accuracy and uniformity in the production of extruded plastic. Automation even more boosts performance, lowering human error and labor costs. The combination of expert system (AI) and machine learning (ML) algorithms is reinventing quality assurance, predicting deviations, and enhancing the general performance of extrusion processes. With the advent of 3D printing, the plastic extrusion landscape is likewise broadening right into brand-new worlds of opportunity. These technological developments are not only enhancing the quality of extruded plastic products however also propelling the industry towards a much more sustainable, effective, and ingenious future.
Real-World Applications of Plastic Extrusion
Plastic extrusion, read here a versatile and effective process, finds use in plenty of real-world applications. It's primarily utilized in the production sector, where it's used to create a myriad of items such as pipelines, tubes, home window frameworks, weather condition removing, and secure fencing. The auto market likewise uses this technology to create parts like plastic and trim bed linen. In addition, the clinical area depends on extrusion for the fabrication of catheters, IV tubes, and other clinical devices. Also in food manufacturing, extrusion contributes in forming products like pasta or grain. The strength and versatility of plastic extrusion, combined with its cost-effectiveness, make it an indispensable procedure across different sectors, underscoring its extensive practical applications.
The Future of Plastic Extrusion: Trends and predictions
As we look to the horizon, it comes to be clear that plastic extrusion is positioned for significant innovations and change. Green options to typical plastic, such as bioplastics, are additionally anticipated to gain grip. These fads indicate a dynamic, developing future for plastic extrusion, driven by technological innovation and a dedication to sustainability.

Conclusion
In final thought, plastic extrusion is a complicated process that uses sophisticated technology and varied products to develop diverse items. As plastic production continues to develop, it continues to be an important component of several markets worldwide.
In significance, plastic extrusion is a high-volume manufacturing process in which raw plastic product is thawed and created into a continuous account.While plastic extrusion is a typically used strategy in production, the products utilized in this procedure substantially affect its last output. At its core, plastic extrusion involves transforming raw plastic material into a constant profiled shape. It has led to the advancement of advanced extrusion equipment, which has great post to read actually improved the performance and high quality of the plastic extrusion procedure.In conclusion, plastic extrusion is a complicated procedure that makes use of sophisticated modern technology and varied products to develop diverse items.